[Parole d'expert] : miser sur la fabrication additive pour réinventer la production industrielle
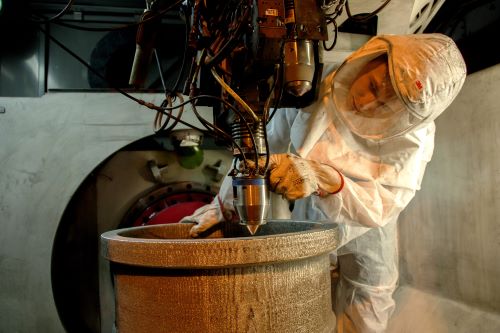
<h3> L’analyse de Philippe Lubineau, directeur du Carnot Cetim</h3> <p> <img alt="" class="img_left" src="/sites/default/files/images/editeur/Philippe%20Lubineau%20%C2%A9Bruno%20Cohen%20%284%29.jpg" style="width: 150px; height: 230px;" />La crise sanitaire a rappelé l’importance de la résilience et de l’adaptation des systèmes productifs. Dans cette optique, la fabrication additive a été citée à de nombreuses reprises comme étant une technologie en capacité de répondre à cette flexibilité, qu’il s’agisse de "mass customisation" (1) ou d’une production relocalisée au plus près des besoins. </p> <p> Technologie numérique par définition, la fabrication additive englobe les procédés de fabrication de pièce par ajout de matière couche par couche et à partir d’un fichier numérique 3D, à l’inverse des méthodes de fabrication soustractive et de fabrication mise en forme. Le développement de la normalisation est par ailleurs un cadre important permettant la diffusion industrielle d’une technologie et son appropriation par les acteurs économiques.</p> <p> <em><span class="tres_petit">(1) La customisation de masse est un processus industriel utilisant des technologies et méthodes de management pour produire une multitude de variétés de produits par leur personnalisation afin de répondre rapidement à la demande des consommateurs. </span></em></p> <h4> </h4> <h4> </h4><p> <strong>La fabrication additive : nouvelles perspectives de production industrielle</strong> </p><p> La fabrication additive permet de changer le paradigme de conception et de fabrication des pièces. Alors que l’on raisonnait par enlèvement de matière, on peut envisager maintenant de nouvelles conceptions basées sur l’ajout de matière, et en optimiser la réalisation en ne mettant le matériau qu’aux seuls endroits requis par la tenue en service par exemple. En 2017, une étude prospective sur le futur de la fabrication additive a été conduite dans le cadre du Pipame. Elle avait pour objectif "d’analyser le positionnement et les conditions de développement de la fabrication additive en France et dans ses territoires, à la fois sur le marché grand public et au sein des filières industrielles et de leurs processus productifs".</p> <p> Elle souligne que "les répercussions de cette révolution technologique se font ressentir à tous les niveaux de la chaîne de valeur : fabricants de machines, sous-traitants, donneurs d’ordres, transporteurs, développeurs de logiciels, fournisseurs de matériaux etc.". La fabrication additive offre ainsi un accès à une technologie permettant de traiter la demande du client avec une offre personnalisable à souhait, voire de procurer la possibilité de produire par lui-même ce qu’il souhaite. Cette étude met en évidence quatre modèles économiques envisageables :</p> <ol><li> Prototypage et expérimentation pour une production améliorée sans modifier la chaîne logistique ; </li> <li> Industrialisation de la personnalisation en réponse à la demande individualisée des clients ; </li> <li> Production série et gain de performance pour une augmentation de la capacité d’innovation produit (formes complexes, nouvelles fonctions intégrées) ;</li> <li> Évolution de la chaîne de valeur avec augmentation de la qualité de service combinée à une mobilité nouvelle des outils de production (gain de compétitivité…). </li> </ol><h4> Le marché de la fabrication additive </h4> <p> La France et les Instituts Carnot, notamment, sont très présents et actifs dans la normalisation internationale sur ce sujet. Le développement des normes internationales adresse les différentes étapes du cycle de vie, de la conception à la caractérisation des procédés, en passant par l’hygiène et la sécurité. Elles s’appuient largement sur des travaux scientifiques lorsqu’il s’agit par exemple d’aspects traitant de la modélisation, de la définition des propriétés d’écoulements des poudres, des effets de l’anisotropie dans les propriétés mécaniques des pièces, des représentations géométriques etc. </p> <p> Après un déclin en 2009, la fabrication additive industrielle a poursuivi sa croissance durant dix ans. Cette croissance annuelle moyenne a été proche de 25 % sur la période 2015-2018. Le marché mondial de la fabrication additive a atteint près de 9,8 Md€ (2).</p> <p> <em><span class="tres_petit">(2) Source : étude Wholer de 2019.</span></em><br /> </p> <h4> La fabrication additive, une technologie clé</h4> <p> <img alt="" class="img_right" src="/sites/default/files/images/editeur/cartographie_FA.png" style="width: 400px; height: 138px;" />La fabrication additive est une des technologies clés de l’industrie du futur, qui permettra de répondre aux nouveaux enjeux industriels de création de valeur à court, moyen et long termes. Depuis novembre 2016, le paysage de la recherche en fabrication additive en France n’a cessé d’évoluer vers plus de structuration et d’interactions. </p> <p> Les Instituts Carnot, réunis au sein de la filière Carnot manufacturing, ont par ailleurs élaboré la première cartographie des acteurs français de la R&D dans le domaine et sont au cœur de cette coordination avec comme objectif de rechercher les synergies et d’éviter l’émiettement des ressources privées et nationales sur des sujets parfois redondants. </p> <h3> Illustration de l'offre de fabrication additive industrielle des instituts Carnot<br /> </h3> <p> <strong><a href="/fr/institut-carnot/cetim" target="_blank">Institut Carnot Cetim</a> : ResMed - Réalisation d’orthèses (personnalisation du design) compatibles avec les nouvelles techniques de prises d’empreintes optiques sur le marché (scanner intra-oral et imagerie 3D) </strong><br /> ResMed est une PME présente en France qui compte environ 200 personnes et qui fabrique une orthèse permettant de traiter la problématique de l’apnée du sommeil. Elle l’a développée en partenariat avec le Carnot Cetim. La fabrication additive s’est avérée être la solution technologique permettant de garder les emplois en France, d’augmenter les volumes pour subvenir aux besoins croissants en France mais également à l’international. <br /> Cette transformation a nécessité des travaux dans le cadre d’un projet de R&D partenariale. Les travaux menés en commun ont permis de définir le couple matériau/procédé, avec un matériau adapté au procédé, qui soit suffisamment résistant aux contraintes biomécaniques de la mâchoire et biocompatible, de pouvoir réduire le nombre de pièces en passant de 20 à 4 pièces assemblées, garantissant une plus grande résistance mécanique. C’est un bel exemple d’un processus qui évolue vers le tout numérique à partir de l’utilisation d’un scanner intra-oral. </p> <p> <a class="lien_video" href="https://www.youtube.com/watch?v=IBCOYNEmZrA&list=PLQRNALlh3Z8FSWD_1EzZW…; target="_blank">Voir la vidéo pour en savoir plus</a></p> <p> <img alt="" class="multi" src="/sites/default/files/images/editeur/Cetim.png" style="width: 400px; height: 121px;" /></p> <p> <strong><a href="/fr/institut-carnot/icéel" target="_blank">Institut Carnot Icéel</a> : maintenance rapide en fabrication additive par Stratoconception</strong></p> <p> <img alt="" class="img_left" src="/sites/default/files/images/editeur/ICEEL.png" style="width: 250px; height: 233px;" />La maintenance industrielle est un secteur peu visible mais qui a pourtant une importance stratégique et économique de premier ordre pour bon nombre de secteurs industriels et en particulier celui des transports. Les apports des technologies de la fabrication additive à ce secteur ont encore été peu étudiés. <br /> En effet, ces nouvelles technologies de fabrication additive peuvent être une réponse pertinente pour améliorer les performances globales des processus d’approvisionnement en pièces de rechange. Pour être efficiente, la fabrication rapide de pièces de maintenance doit reposer sur une filière complète qui est la traduction de la chaîne numérique intégrée et continue pour la conception rapide de produits adaptée aux enjeux de la maintenance. </p> <p> Le Cirtes (Centre européen de développement rapide de produit), composante du Carnot Icéel, a depuis plusieurs années travaillé avec ses partenaires et particulièrement la SNCF, sur différents concepts et scénarios de fabrication additive de pièces métalliques par Stratoconception® pour la maintenance. Parmi les pistes explorées, citons notamment la fabrication directe métallique (exemple d’un palier en acier pour la SNCF) et la fabrication d’outillages rapides légers. L’analyse des pièces potentielles, ainsi que des filières à déployer, ont permis de réaliser des pièces testées en conditions et de comparer les scénarios.</p> <p> <em><span class="tres_petit">Copyright : Pièce test en Stratoconception® Métal après tests (Source SNCF)</span></em></p> <p> <strong><a href="/fr/institut-carnot/CEA-LIST" target="_blank">Institut Carnot CEA LIST</a> : contrôler les pièces pendant la production devient possible </strong></p> <p> Pour produire des pièces de formes extrêmement complexes, la fabrication additive est de plus en plus utilisée. Afin de garantir l’absence de tout défaut, un nouveau procédé de contrôle en production vient d’être mis au point par le Carnot CEA LIST.</p> <p> La technologie de fabrication additive DED (Directed Energy Deposition ou dépôt sous énergie concentrée) permet la production, par couches successives, de pièces en métal, en polymère ou encore en céramique. Dans ce procédé, une énergie thermique focalisée est utilisée pour fusionner des matériaux, poudre ou fil, en les fondant au fur et à mesure qu’ils sont déposés grâce à un faisceau laser ou d’électrons. Cette technique de fabrication additive permet de réaliser des pièces de formes complexes impossibles à obtenir par des procédés conventionnels. Elle est aujourd’hui de plus en plus utilisée dans les industries automobile, aéronautique et médicale notamment, pour lesquelles les pièces doivent être exemptes de tout défaut. Le Carnot CEA List vient de mettre au point un moyen de traquer l’apparition de la moindre micro-porosité ou fissuration, en cours même de fabrication.</p> <p> Ce procédé consiste à utiliser un laser pulsé pour générer des ondes élastiques, à la fois en surface et en profondeur de l’objet en formation, puis à les détecter avec un autre laser par interférométrie. Les éventuelles anomalies de propagation sont la signature de la présence de défauts. Les chercheurs ont relevé le défi de synchroniser la trajectoire du robot-sonde avec celle du robot de fabrication additive et de permettre ainsi la détection de défauts de l’ordre de la centaine de microns.</p> <p> <a class="lien_video" href="https://youtu.be/0A8sAJLUEZs?list=PLArmu-xMLSodeMKdeNrzH34pRtSRtSW_j&qu…; target="_blank">Voir la vidéo pour en savoir plus</a><br /><em><span class="tres_petit">Copyright : Shutterstock et Adobe Stock</span></em><br /><img alt="" class="img_left" src="/sites/default/files/images/editeur/FA_CEA%20LIST.png" /></p> <p> </p> <p> </p> <p> </p> <p> </p> <p> <strong><a href="/fr/institut-carnot/mines" target="_blank">Institut Carnot M.I.N.E.S </a>: Vers des pièces céramiques « imprimées » </strong></p> <p> La fabrication additive par fusion de céramiques est en passe de conquérir de nombreuses industries. Des chercheurs de l’Institut Carnot M.I.N.E.S viennent de fabriquer, couche par couche, une aube de turbine dans un matériau sensible aux chocs thermiques et qui intéresse fortement le secteur aéronautique.<br /> Une petite révolution est en train de naître dans le milieu de la mise en forme par voie liquide de matériaux fragiles à haut point de fusion. La fabrication additive – version industrielle de l’impression 3D – permettra bientôt de fabriquer plus rapidement, sans reprise d’usinage et à un coût moindre des pièces céramiques de géométries complexes, à la microstructure orientée.<br /> Cette révolution concerne de nombreuses industries, comme l’aéronautique, le spatial, le médical… Mais auparavant, il convient de mieux maîtriser la fabrication de pièces basées sur ces matériaux céramiques, afin d’obtenir une microstructure exempte de défauts et ainsi améliorer, dans un premier temps, leurs propriétés.</p> <p> L’objectif est d’atteindre puis de dépasser le niveau des pièces actuellement réalisées dans ces mêmes matériaux, produits par les méthodes de fabrication traditionnelles issues de la coulée. C’est l’objet du projet CEFALE (Fabrication additive de pièces CEramiques hautes performances par Fusion lAser séLEctive), financé par l’Institut Carnot M.I.N.E.S, qui vise à améliorer les procédés de fabrication additive directe de pièces en céramique à base d’oxydes métalliques.<br /> Une telle avancée a été rendue possible grâce à un travail en commun de chercheuses et chercheurs pluridisciplinaires : spécialistes des poudres, de la conception assistée par ordinateur, de la thermique, de la mécanique et également de la simulation numérique des procédés. </p> <p> L’entreprise Safran est particulièrement intéressée par de telles activités de recherche. </p> <p> <img alt="" src="/sites/default/files/images/editeur/fabricationadditive_MINES.png" style="width: 300px; height: 167px;" /><br /><em><span class="tres_petit">Copyright Mines ParisTech</span></em></p> <p> <strong><a href="http://u/fr/institut-carnot/il" target="_blank">Institut Carnot Ingénierie@Lyon</a> : Fabrication additive métallique, une chaine de valeur inédite de la poudre aux post-traitement et la caractérisation fine des structures et du comportement</strong></p> <p> Toute la chaîne de valeur de la fabrication additive métallique doit être fiabilisée et optimisée, afin d’atteindre les standards industriels d’une production automatisée. La complémentarité des acteurs Carnot Ingénierie @ Lyon, en étroite collaboration avec le consortium initiative3D et soutenue par la région AURA, est un atout majeur pour lever les verrous actuels.</p> <p> La fiabilisation du process passe par de nouvelles règles de conception, le design et l’élaboration d’alliages et de poudres adaptés au procédé, leur recyclage, l’optimisation des procédés eux-mêmes dont plusieurs technologies sont présentes au sein de l’institut. Cette optimisation passe par le développement de simulations multi-physiques ou encore d’un monitoring et d’un pilotage des procédés. Une fois les pièces fabriquées, la métallurgie et les états de surfaces résiduels doivent être optimisés pour garantir une durée de vie acceptable en service, notamment en fatigue. Des traitements thermiques adaptés et des moyens de parachèvement de surface sont développés. Les moyens de caractérisation des défauts propres à la fabrication additive métallique doivent eux-aussi être adaptés (tomographie aux rayons X, moyens de CND). Cette chaine de valeur présente au sein de l’Institut Carnot Ingénierie @ Lyon permet de prendre en charge la fabrication additive métallique dans toutes ses composantes. <br /> Cette complémentarité a été validée et démontrée en environnements représentatifs dans le projet MELTED, financé par l’institut. La technologie choisie rend optimale la conception des moules d’injection plastique par mise en place de canaux de refroidissement au plus proche des surfaces à refroidir. Il en résulte une réduction des défauts lors du refroidissement des pièces injectées et une diminution du temps de cycle. Le projet MELTED a démontré une augmentation de la limite d’endurance de 25% par traitement de parachèvement des canaux internes.</p> <p> La montée en TRL des recherches menées au sein de l’institut Carnot Ingénierie @ Lyon dans le domaine de la fabrication additive est facilitée d’une part par l’intégration du centre technique IPC et plus récemment de la plateforme MANUTECH USD et, d’autre part, par la richesse industrielle de la région AURA. Le projet AMI AURA OCIM3D en partenariat avec la société PCI est un exemple de diffusion des savoir-faire en direction de l’écosystème industriel.</p> <p> <a class="lien_video" href="https://www.youtube.com/watch?v=ZugPoLw9_Do" target="_blank">voir la vidéo pour en savoir plus</a></p> <p> <img alt="" class="multi" src="/sites/default/files/images/editeur/2020_04_20_Articles_IatL_Figures.jpg" style="width: 300px; height: 225px;" /></p> <p> <strong>Institut Carnot Mica : industrialiser la fabrication additive de grandes pièces </strong></p> <p> L’association des technologies de dépôt de fil et de dépôt de poudre est une des solutions approchées pour traiter les problématiques économiques liées à la fabrication additive des pièces de grandes dimensions. Le projet Pamprod (Procédés Additive Manufacturing – PRODuctivité) développé par le Carnot Mica dans le cadre de l’action Carnot filière AirCar, vise la conception d’une machine hybride et, plus largement, la création d’une plate-forme de fabrication additive industrielle.</p> <p> Pour garantir la performance de dépôt et sa qualité finale, tout un système de contrôle de procédés en lien avec la simulation thermo-mécanique alertera l’opérateur en cas de dysfonctionnement des procédés. L’opérateur pourra alors intervenir à tout moment pour ajuster les paramètres opératoires. À terme, la machine doit pouvoir avoir une autonomie relative. "Nous allons pouvoir suivre chaque phase, chaque couche et agir à chaque variation des paramètres", explique Jean-Paul Gaufillet, président d’Irepa Laser au sein du Carnot Mica, partenaire industriel du projet avec Aperam Alloys, Prodways Rapid Additive Forging et Supratec Evo et des partenaires académiques de l’université de Lorraine comme l’Institut Jean Lamour et l’Estia. </p> <p> La fabrication additive présente en général aujourd’hui une rentabilité limitée à quelques applications. "Sur cet aspect, le projet Pamprod permettra d’obtenir un coût d’exploitation plus en phase avec le marché. Tous les indicateurs vont actuellement dans le bon sens : l’objectif des 800 cm3/h de matière déposée est atteint, ce qui est une belle performance en soi. Passer à plus de 1 000 cm3/h est réaliste", espère-t-il.</p> <p> Dans le cadre de ce projet, l’obligation de résultats visée impose de réaliser une machine opérationnelle qui réponde aux exigences du marché des grandes dimensions. L’approche marketing, la diffusion, la commercialisation sont des aspects qui ont pesé lourd dans la balance pour obtenir le soutien de BPI et de l’action Carnot filière AirCar. Ce projet est une vraie démarche entrepreneuriale et apporte son éco à l’offre fabrication additive Grand Est "AddAGE". </p> <h3> Nouvelles perspectives : l’impression 4D</h3> <p> Combiner le procédé de fabrication additive et l’utilisation de matériaux "programmables" pour obtenir des produits capables de changer de couleur, de forme ou de texture au cours du temps en fonction des conditions extérieures ou de sollicitations physiques : température, humidité, lumière, magnétisme, contraintes mécaniques. Tels sont les enjeux de la fabrication additive 4D, ou impression 4D. Le comportement futur du produit pourra donc être préenregistré soit au sein de la brique matériau, soit au cours du procédé de fabrication.</p> <p> Ces nouvelles fonctionnalités ne sont envisageables que, d’une part, par la maîtrise de nouveaux matériaux, assemblages hétérogènes interactifs, réseaux de fibres, polymères électro-actifs, élastomères à cristaux liquides, composites à mémoire de forme et, d’autre part, par la mise en algorithmes des lois physiques à programmer dans ces matériaux, ce qui conduit à l’intégration d’intelligence artificielle dans les processus de conception/fabrication. </p> <p> Les perspectives sont prometteuses, en particulier l’impression 4D du vivant ou bio-impression, dans laquelle les sciences biologiques, chimiques et des matériaux, ainsi que l’ingénierie des procédés, occupent une place prépondérante. Quelques autres exemples d’applications diverses : matériaux autoréparants, canalisations intelligentes changeant de forme en fonction de paramètres de fonctionnement, panneaux solaires plus légers pour les satellites, ceux-ci pouvant se déployer sans l’aide de mécanismes énergivores, etc.</p> <h4> FORTE CROISSANCE ANNUELLE MONDIALE</h4> <p> Cette approche reste encore principalement limitée à des pièces de plus petites tailles malgré un intérêt vif pour la construction de structures déployables de très grandes tailles en milieu extrême (exploration spatiale avec le déploiement d’antennes, de stations spatiales…). Cette limitation est en partie due aux cinétiques des modifications qui restent lentes sur des pièces à volume important, mais qui sont très rapides sur des pièces à l’échelle micro voir sub-micrométrique. </p> <p> Le marché de l’impression 4D, encore en développement, reste très segmenté, selon les applications industrielles : aéronautique et spatial, automobile, textile, construction, défense, santé et services publics.</p> <p> En 2019, les projections envisageaient au niveau mondial une croissance annuelle moyenne de l’ordre de 43 % pour atteindre environ 540 M$ en 2025 (495 M€). Dès aujourd’hui, les acquis de base de cette nouvelle branche technologique rendent possible la réalisation d’objets imprimés à partir de systèmes d’imprimantes 3D évolués et de matériaux existants, mais l’essentiel de la révolution 4D dédiée à la création d’objets intelligents et autonomes à vocation industrielle est encore à venir.<br /> </p>